Creep filling machines have become a staple in liquid packaging industries due to their ability to accurately and efficiently fill containers with various liquids. In this article, we will delve into the working principles and functionalities of creep filling machines, highlighting their role in achieving high-quality liquid packaging.
Understanding Creep Filling Machines
- Basic Function:Creep filling machines are designed to precisely fill containers with liquid products. They utilize a volumetric filling method that ensures consistent and accurate fills, accommodating a wide range of container sizes and liquid viscosities.
- Versatility:Creep filling machines can handle a variety of liquids, including water, beverages, oils, chemicals, pharmaceuticals, and personal care products. Their adaptable nature allows them to be used in diverse industries, such as food and beverage, cosmetics, pharmaceuticals, and household goods.
Working Principles of Creep Filling Machines
- Container Placement
The containers to be filled are placed on the machine’s conveyor system or indexing mechanism, which moves them through the filling process. - Container Centering
To ensure accurate filling, creep filling machines often incorporate centering mechanisms that position containers precisely beneath the filling nozzles. This helps minimize product spillage and achieve consistent fills. - Filling Nozzles
Creep filling machines are equipped with multiple filling nozzles, usually made of stainless steel, which are responsible for delivering the liquid into the containers. The number of nozzles can vary depending on the machine’s design and production requirements. - Volumetric Filling
Creep filling machines employ a volumetric filling method, where the liquid is measured by volume rather than weight. This is achieved through the use of pistons, pumps, or flow meters that accurately dispense the desired amount of liquid into each container. - Control Systems
Creep filling machines feature advanced control systems that regulate the filling process. These systems typically include adjustable settings for fill volume, filling speed, and other parameters, allowing operators to fine-tune the machine to meet specific packaging requirements.
Filling Process and Operations
- Start and Stop
Once the containers are correctly positioned, the operator initiates the filling process by activating the machine. The filling operation can be triggered manually or automatically, depending on the machine’s configuration. - Liquid Dispensing
As the containers move beneath the filling nozzles, the liquid is dispensed into them. The filling nozzles release the predetermined volume of liquid, ensuring accurate fills and minimizing wastage or overfilling. - Anti-Drip Mechanism
To prevent product dripping or spillage after the filling process, creep filling machines often incorporate anti-drip mechanisms. These mechanisms retract the filling nozzles or employ vacuum suction to remove any excess liquid, maintaining clean and tidy packaging. - Quality Control
Creep filling machines may include additional features for quality control, such as checkweighers or vision systems. These systems can verify fill accuracy, detect container defects, or ensure proper labeling, contributing to overall product quality and compliance.
Creep filling machines offer an efficient and precise solution for liquid packaging across a range of industries. By utilizing a volumetric filling method and advanced control systems, these machines ensure consistent and accurate fills, peristaltic filling machine minimizing product waste and optimizing production efficiency. With their versatility and ability to handle various liquid viscosities, creep filling machines have become indispensable tools for achieving high-quality liquid packaging in diverse manufacturing environments.
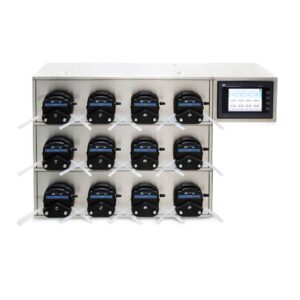